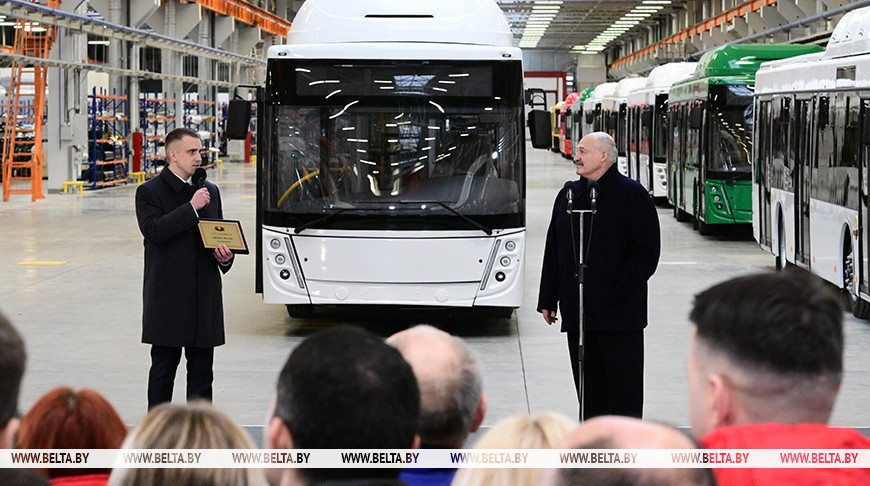
News of the story
"After the Fact: Lukashenko’s Decisions"
Minsk Automobile Plant has experienced a lot in its long history. It will be even difficult to find words to describe it. In its early years, the plant, which was built during World War II, assembled German vehicles. Later it assembled U.S. vehicles Ford, Chevrolet, and Studebaker. In the post-war time, the plant produced haulers unmatched in the automaking industry both in the Soviet Union and across the globe. Belarusian trucks were awarded the Grand Prix of the Brussell World’s Fair. During the “perestroika” [restructuring] period Minskers again surprised the motor transport community by presenting their famous concept vehicle MAZ-2000. This year MAZ once again opened a new chapter in its history. The enterprise has completed the construction of a bus plant and launched the production of passenger vehicles. In a new episode of BelTA's YouTube project “After the Fact: Lukashenko's Decisions” we will show you the new bus plant, describe its features and talk to its workers. We will show you Aleksandr Lukashenko’s visit to MAZ and the results of the presidential inspection. We will tell you why Belarusian buses are praised everywhere and why they are a source of pride for the head of state and all of us.
Why was a new bus plant built in Minsk?
Minsk Automobile Plant started the major overhaul of its bus production facility in 2023. It took a year and a half to build a new site from scratch. More than Br300 million were invested in the project. Why did the enterprise decide to build a new plant? Wouldn’t some repair and upgrade have been enough?
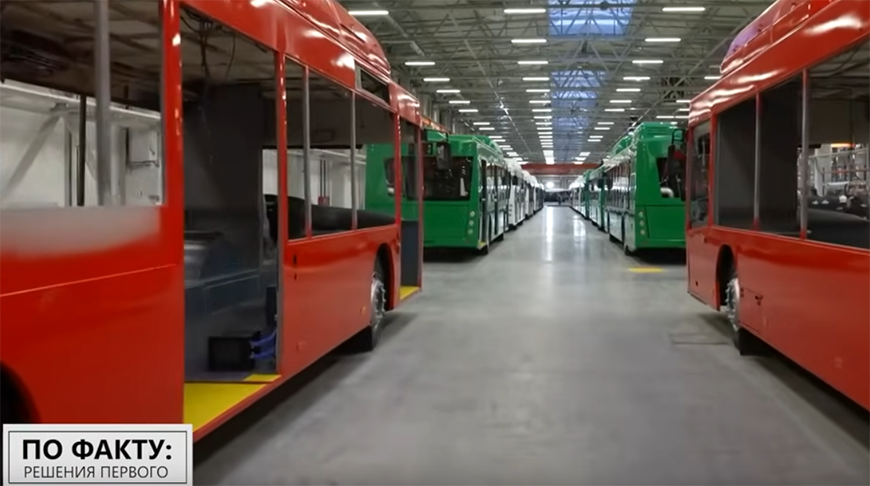
MAZ had been successfully producing passenger vehicles, but the former plant actually consisted of six workshops located in absolutely different places. Thus, a bus body was assembled in one place, painted in another, got handrails installed in the third one and so on. The bus had to be constantly transported from place to place during its assembly. There is little efficiency in this, isn’t it? Today MAZ has its entire technological cycle under one roof.
“The final assembly area features three assembly lines. There used to be one line only. Before, buses were moved between the workshops, which in winter, with all the precipitation, had a negative impact on the assembly and quality of buses. Now everything is different. We have a large model range of vehicles (medium- to large-sized solutions). Three lines enable us to assemble several models simultaneously,” chief engineer of the bus plant Aleksandr Niskoromny said.
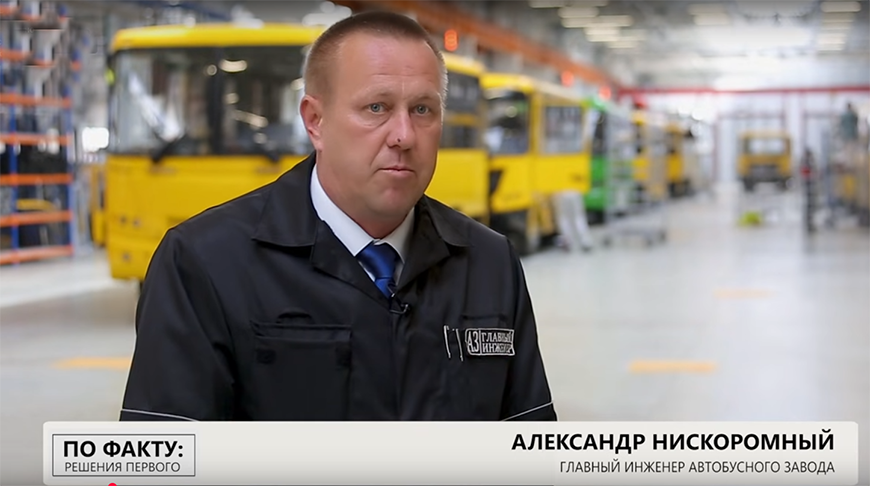
Just estimate the scale: the area of the bus welding and assembly shop is over 32,000 m2. This is eight football fields! The total area of the plant is more than 40,000 m2. How many countries can boast such production? While city buses are assembled in many countries in the post-Soviet space, tourist-class models are produced only in Minsk today. Today MAZ passenger vehicles are available in 15 models and 30 modifications. The enterprise’s truck lineup consists of 600 models.
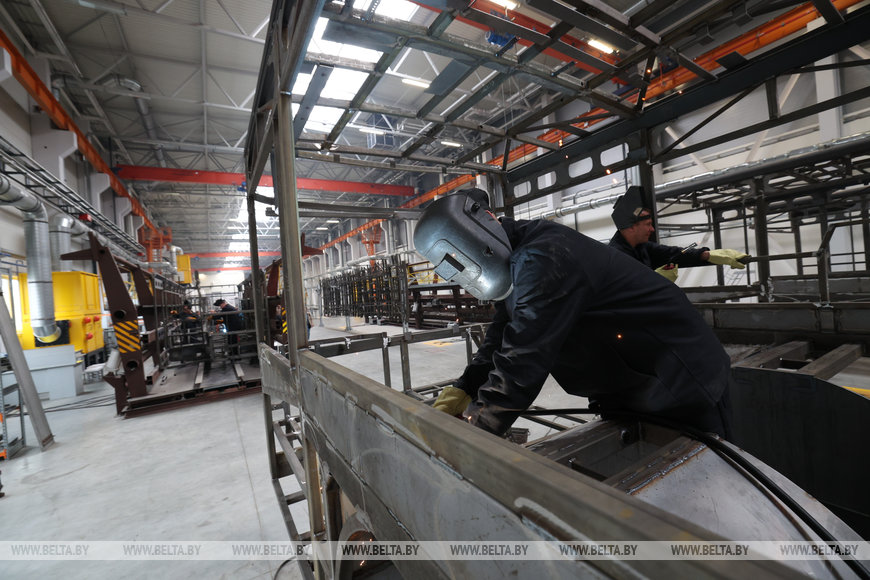
Aleksandr Solomakho, the head of the bus welding and assembly shop, says that the time of assembling depends on the vehicle model. For example, a medium-class bus will need nearly 1,000 standard hours to be assembled. A three-axle intercity bus will need more than 4,000 standard hours.
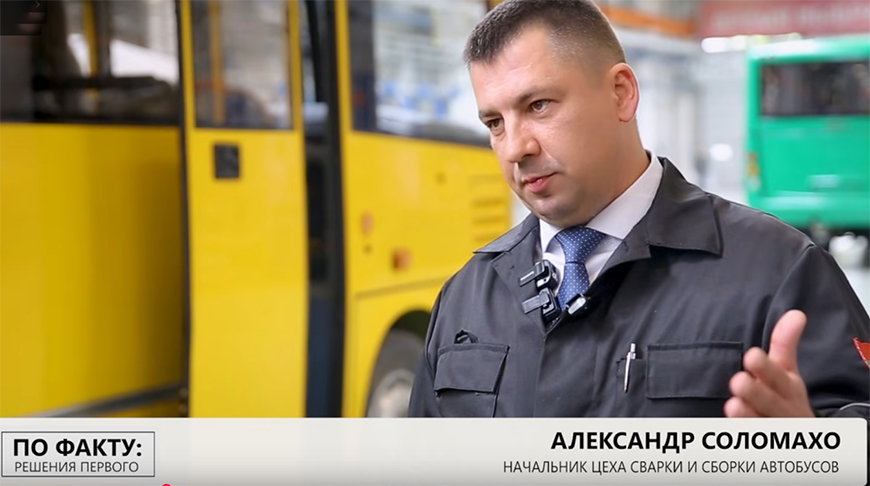
“These three conveyors ensure uninterrupted assembly. This conveyor is fast, that one is slow, and the third one is slower. Or vice versa. Everything depends on orders and production plan,” he said.
The new production facility differs a lot from the previous one. Mikhail Melnik is an assembly fitter at the plant. He says that there is a lot of light and space in the workshops. “There are showers and lock rooms here. The equipment is better,” he said.
When he worked at the old plant, Mikhail decided to quit and work for a private company. He thought he would earn more. However, everything turned out differently. “The private company did not pay at all. Private business just wants to earn more and do not pay its workers,” he said.
Mikhail came back to work at MAZ. He and his wife has recently welcomed a child. Every time they get on a bus, the young father says to his child that he has also contributed to its production. “I tell my child than maybe I assembled it, too. The child is still very small and just smiles listening to me,” the plant worker said.
How are Belarusian buses assembled?
At the start of the year, the president got familiar with the reconstruction process at the enterprise to see how ready the production facility and specialists were to start operation.
The new plant of more than 40,000 m2 features a bus welding, painting and assembly shop, a welding, blanking and mechanical workshop. The bus production process involves several stages: welding the frame, mounting, straightening and priming, installing the powertrain, assembling the body, applying filler and preparing for painting, automated painting and drying, and finally assembling the interior. After quality control, the finished passenger vehicles are handed over to the sales department.
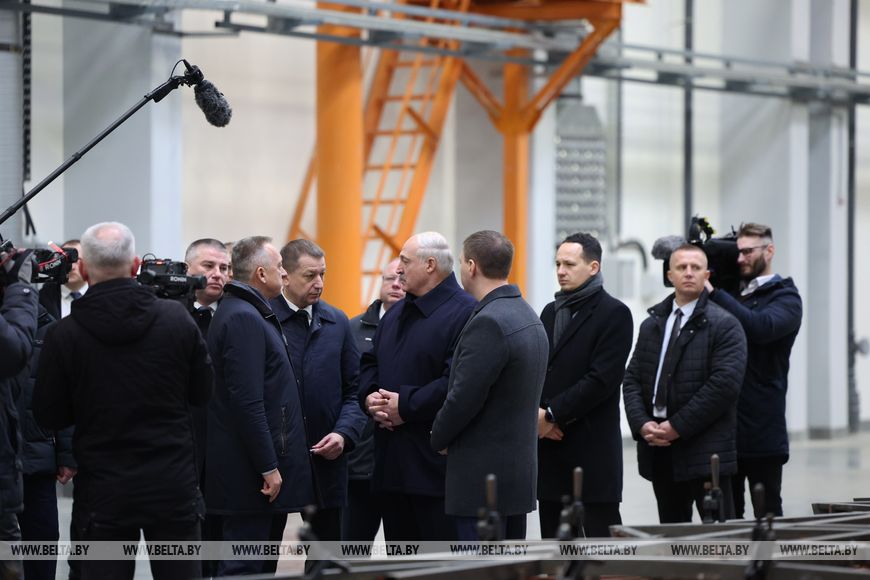
The president compared this production process to aircraft manufacturing. The reason lies in the fact that such equipment is not created on a conveyor belt or using robotic systems, as is common in car production. It is largely unique craftsmanship.
By the way, why not actually use robots to assemble buses? As the chief engineer explained, it all comes down to volume.
“First, the individual parts of the frame are welded: the roof, base, side panels, front, and rear. Then, all these components are placed into the main assembly facility, where the entire frame is welded together. Robotic welding will pay off if the plant produces large volume, at least 15,000 units per year (we plan to reach 3,000 per year). Additionally, we don’t produce just one bus model: we have a wide model range. Programming and adjusting robots for each bus model is a complex process. People, on the other hand, are more adaptable and can quickly switch tasks. Today, a worker welds in one facility, tomorrow in another. The assembly facility is reconfigured within 30 to 40 minutes, allowing us to weld an entirely different frame," Aleksandr Niskoromny said.
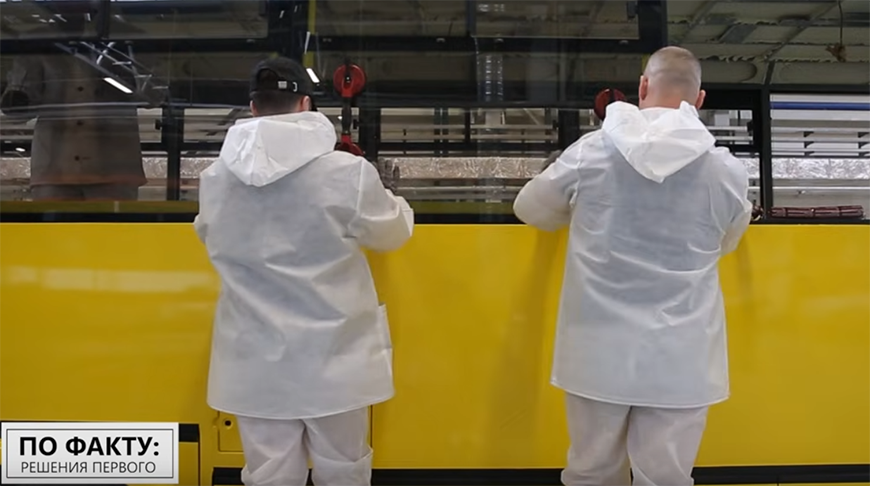
The bus painting includes several stages. First, surface is prepared for painting by grinding, filling, then priming. Before painting, the workers sand the primer and eliminate minor imperfections. Then comes the painting itself.
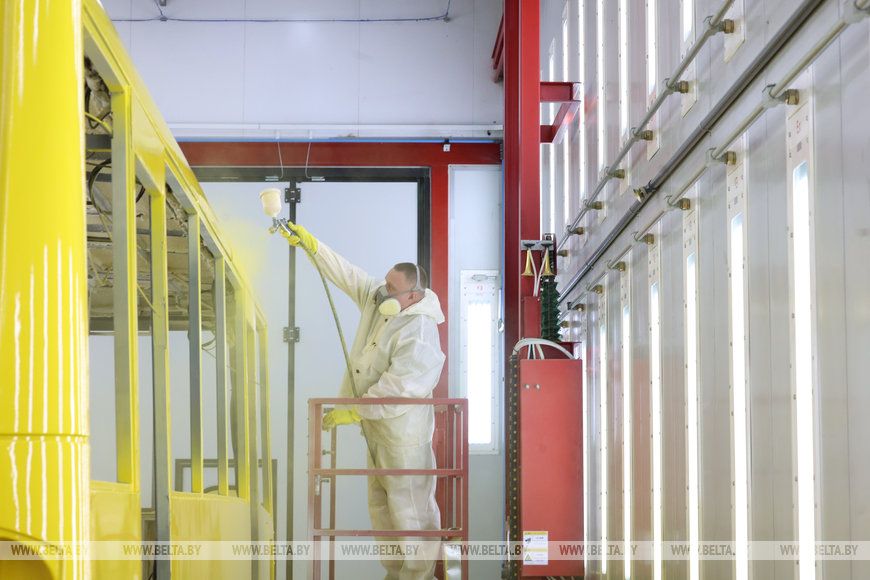
“Now we have huge preparation booths that allow at least 12 to 13 people to work simultaneously. At the old plant, we had only one booth. Now, our painting and drying booths are combined, so buses are dried in the same booth where they are painted. Previously, they had to be moved to another booth for drying. The painting booths here are large and double-sized, meaning we can paint an articulated bus or two smaller buses simultaneously in two booths. We have six of these booths, which significantly boosts our production capacity," senior specialist of the painting section Tatiana Shalai remarked.
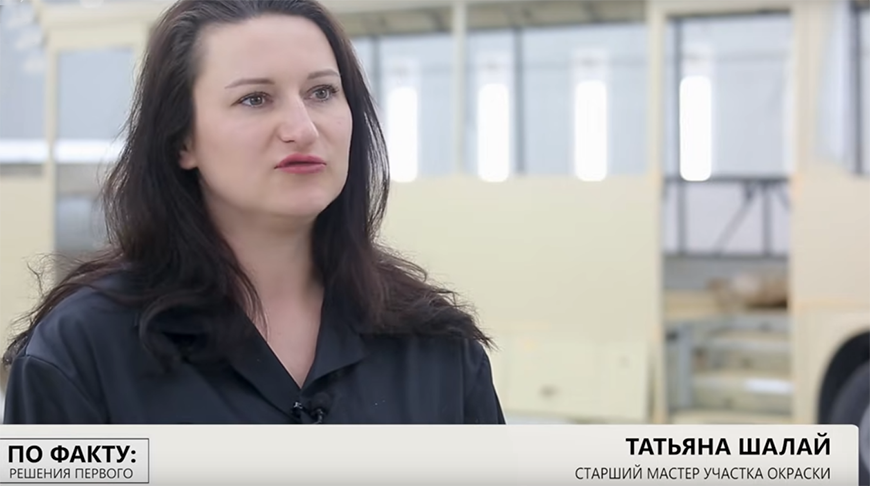
What economic impact is expected from the new facility?
In recent years, MAZ’s annual output has been around 1,500 passenger vehicles. With the construction of the new facility, these figures are expected to double. The company emphasizes that the significance of this production cannot be overestimated, especially amid the global shift toward environmentally friendly transport and stricter technical requirements for passenger transport. It is estimated that by increasing efficiency and producing in-demand diesel, gas and electric vehicles, the added value per employee will range from €78,000 to €108,000. Like in any project, the authorities expect the bus factory to reach profitability, and deadlines have been set. But is it really just about money?
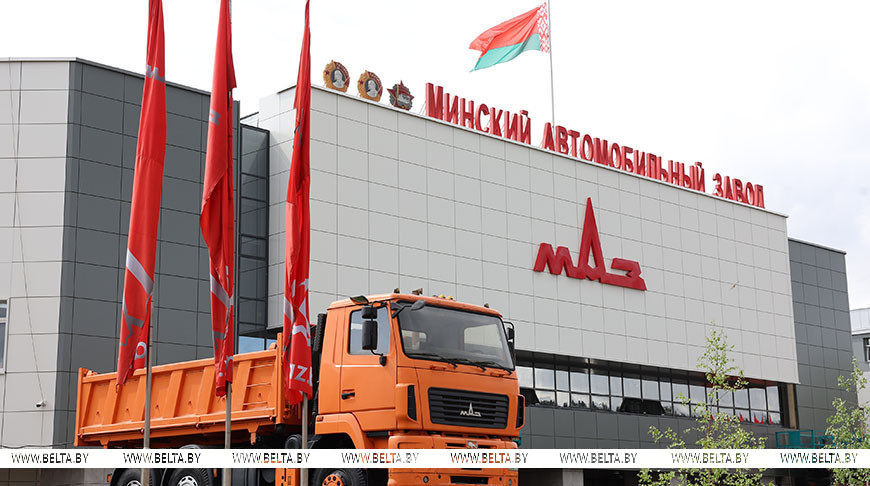
“We are all consumers. We get on buses in the city and observe pensioners, schoolchildren, and students using them. So is this just about business? Or is it a social project? Foreigners visiting Minsk judge our country by the appearance and quality of our public transport. Is this business or a social project?” MAZ Director General Valery Ivankovich asked rhetorically. “An annual capacity of 3,000 passenger vehicles brings a substantial economic impact and, of course, new jobs. This is technological sovereignty in practice.”
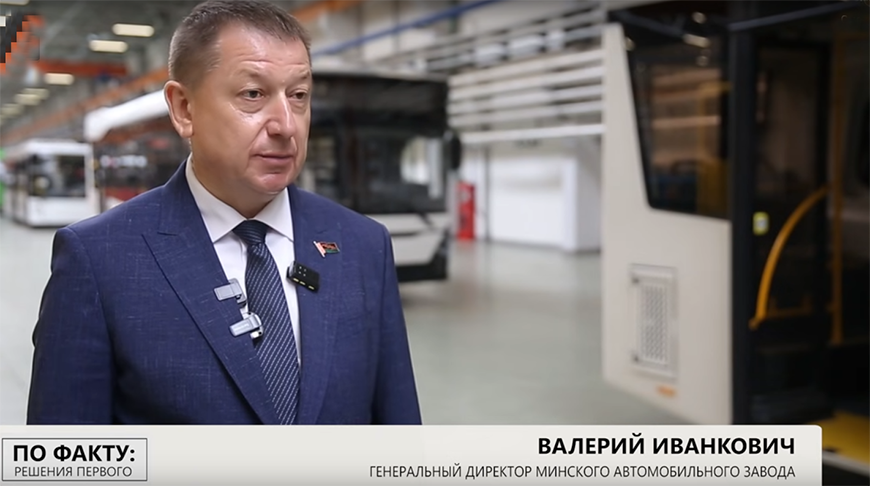
How does the new MAZ bus model differ?
The first bus produced at the new factory, along with another batch, will be sent to Mogilev Oblast. This is a fundamentally new model by Minsk Automobile Plant: the third-generation MAZ 303047 bus. Its key features include a low-floor design, making boarding even more convenient, an ergonomic interior, and the option to install up to 16 passenger seats without ramps underneath them. The expanded glazing area enhances visibility. The most significant advantage is the universal frame. It allows producing various types of passenger transport, including diesel, compressed or liquefied gas, and electric-powered versions. While these new features may not be visible to passengers, they are crucial for buyers.
By 2027, the plant will assemble passenger vehicles of the second and third generations, and then switch to the production of buses of the third generation only.
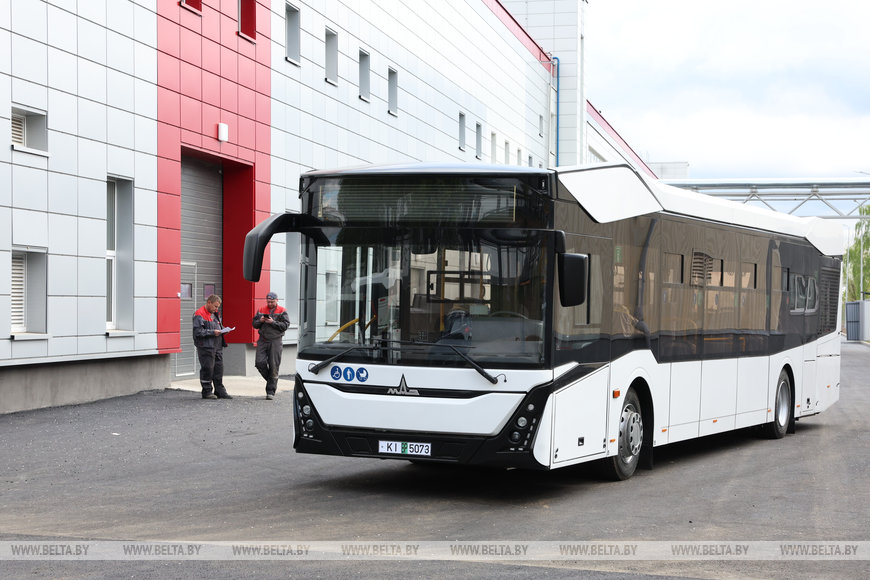
"This new-generation model, the MAZ 303, features enhanced equipment, smoother handling, and a more powerful engine. It is comfortable for both drivers and passengers. The climate control system is excellent. Modern instrument panel. It indicates when doors are open and alerts to any potential faults. Its electronic modules display a green light when functioning correctly. If an issue arises, they turn red," test driver Aleksandr Levdorovich shared his impressions.
Belarus and Russia remain the main sales markets for MAZ. But the task to diversify exports could not be ignored by the enterprise. This year the plant intends to significantly increase supplies to distant countries.
"We do not have a stockpile of unsold vehicles: we produce strictly on order. Every vehicle built in our workshop is already sold. This year, our goal is to deliver over 2,000 units, a fully achievable target. At present, we are filling orders for the third quarter. We have projects and signed contracts with several Latin American, African, and Asian countries. In 2025, we expect a significant increase in exports to distant markets," Vladimir Dormash, deputy commercial director for passenger vehicle sales, said.
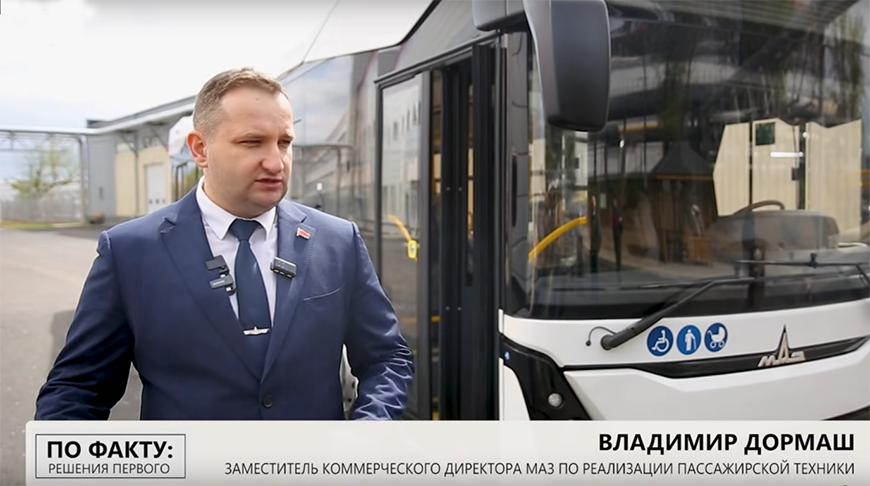
What did Lukashenko call his main presidential task?
At the beginning of the year, during his visit to the new bus manufacturing facility, Aleksandr Lukashenko recalled his previous visit to MAZ. According to him, the conditions the factory staff used to work in were in need of improvement. Didn’t they deserve their own modern factory? The head of state promised to have such a facility built if there is demand for Belarusian buses.
"They say you are on the up and up, and I will be delighted if this presidential project succeeds. I was determined to preserve our industry giants. When my tenure as president just began, I promised myself to preserve everything that had been built by previous generations. And those of you who are older remember: we set off on this big journey together. MAZ, BelAZ, elevators in Mogilev, Integral (its products are in huge demand today), and all other enterprises - all this had to be saved. Frankly speaking (again, I do not want to overpraise you), when I see a MAZ vehicle, our buses, trolleybuses, I feel pride. And I am happy that we have preserved the mechanical engineering industry in our country," the president noted.
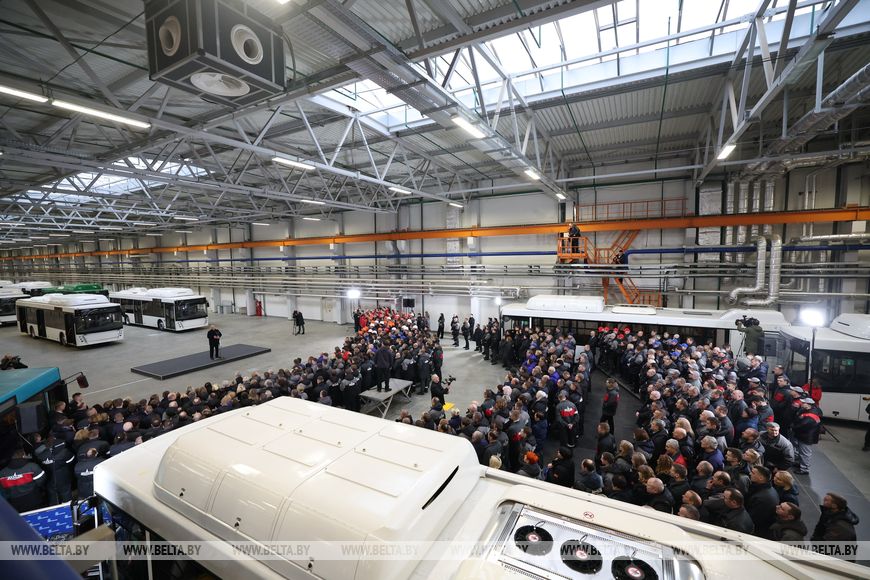
The inauguration of the new MAZ production facility marks not just an expansion in manufacturing capacity but a leap forward in Belarusian engineering. Aleksandr Lukashenko reassures that the state will continue supporting such enterprises, but only if results are delivered.
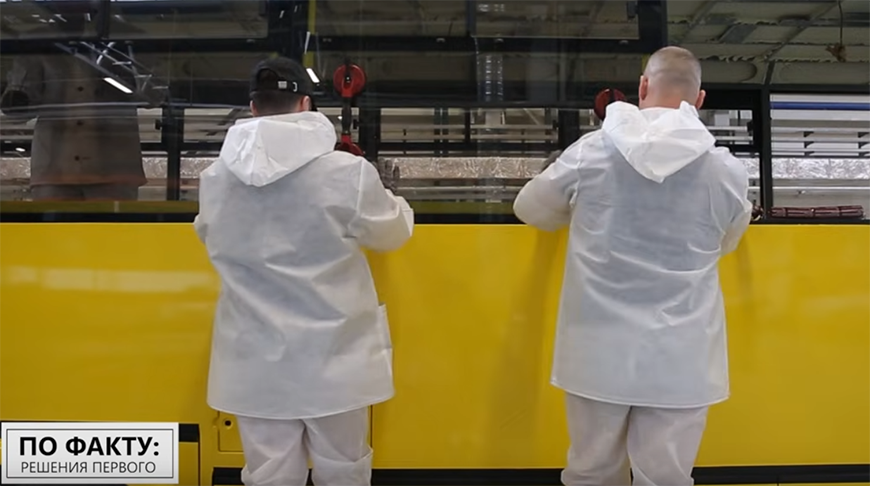
The bus painting includes several stages. First, surface is prepared for painting by grinding, filling, then priming. Before painting, the workers sand the primer and eliminate minor imperfections. Then comes the painting itself.
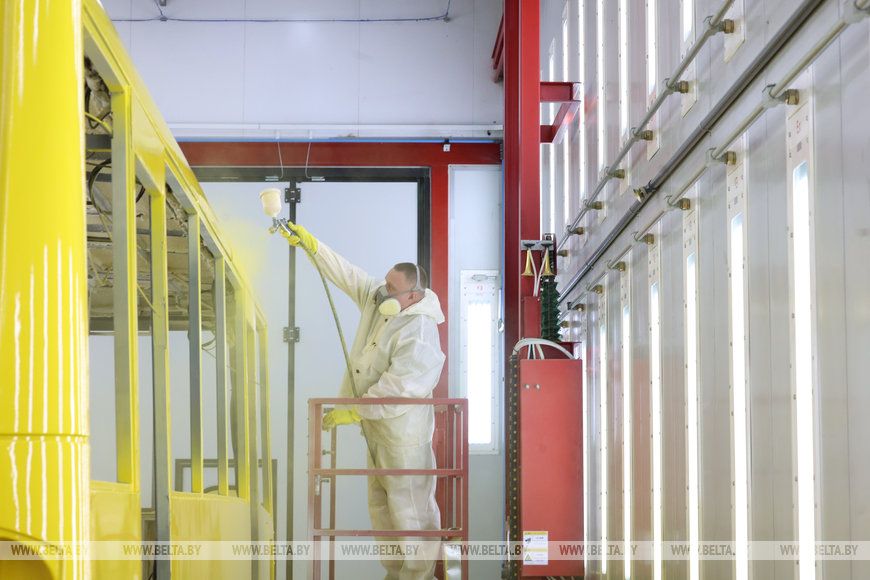
“Now we have huge preparation booths that allow at least 12 to 13 people to work simultaneously. At the old plant, we had only one booth. Now, our painting and drying booths are combined, so buses are dried in the same booth where they are painted. Previously, they had to be moved to another booth for drying. The painting booths here are large and double-sized, meaning we can paint an articulated bus or two smaller buses simultaneously in two booths. We have six of these booths, which significantly boosts our production capacity," senior specialist of the painting section Tatiana Shalai remarked.
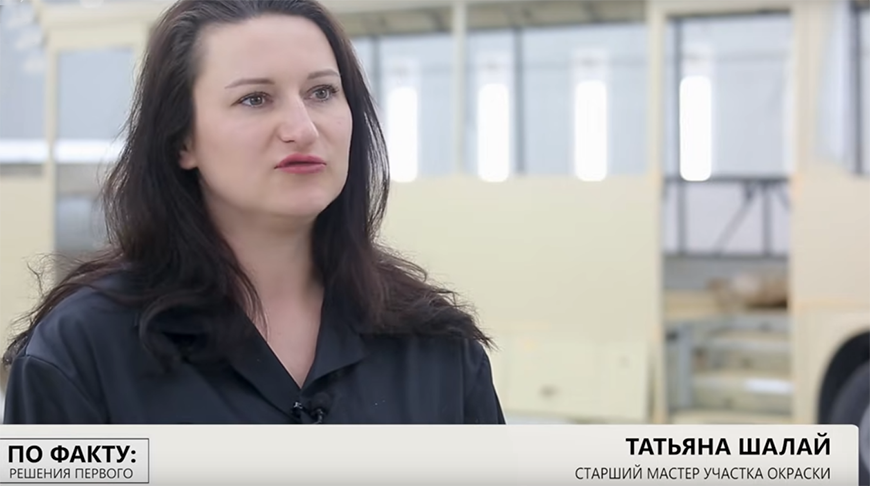
What economic impact is expected from the new facility?
In recent years, MAZ’s annual output has been around 1,500 passenger vehicles. With the construction of the new facility, these figures are expected to double. The company emphasizes that the significance of this production cannot be overestimated, especially amid the global shift toward environmentally friendly transport and stricter technical requirements for passenger transport. It is estimated that by increasing efficiency and producing in-demand diesel, gas and electric vehicles, the added value per employee will range from €78,000 to €108,000. Like in any project, the authorities expect the bus factory to reach profitability, and deadlines have been set. But is it really just about money?
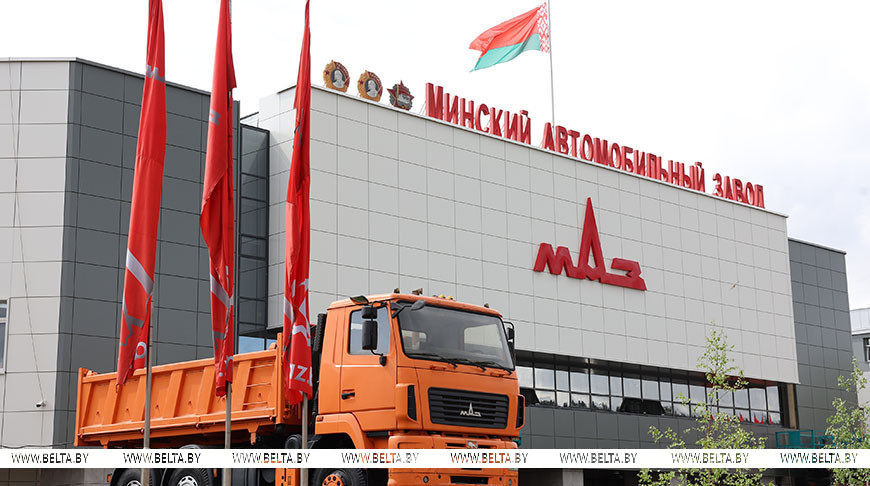
“We are all consumers. We get on buses in the city and observe pensioners, schoolchildren, and students using them. So is this just about business? Or is it a social project? Foreigners visiting Minsk judge our country by the appearance and quality of our public transport. Is this business or a social project?” MAZ Director General Valery Ivankovich asked rhetorically. “An annual capacity of 3,000 passenger vehicles brings a substantial economic impact and, of course, new jobs. This is technological sovereignty in practice.”
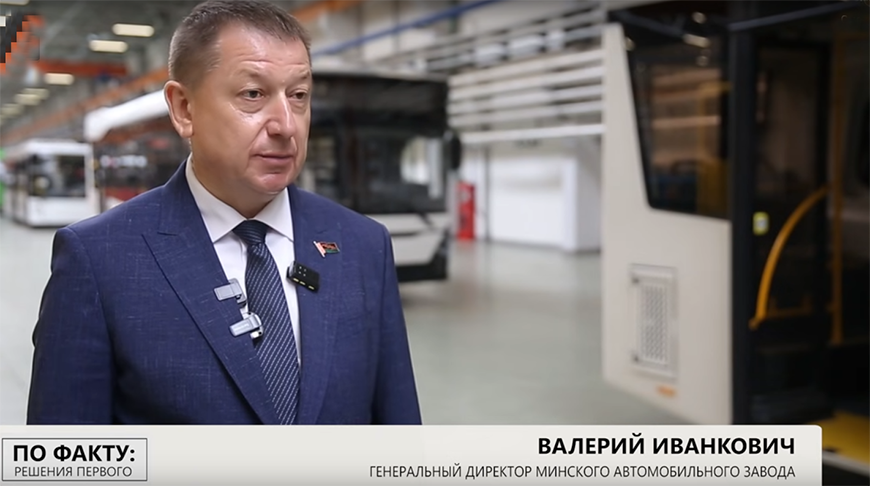
How does the new MAZ bus model differ?
The first bus produced at the new factory, along with another batch, will be sent to Mogilev Oblast. This is a fundamentally new model by Minsk Automobile Plant: the third-generation MAZ 303047 bus. Its key features include a low-floor design, making boarding even more convenient, an ergonomic interior, and the option to install up to 16 passenger seats without ramps underneath them. The expanded glazing area enhances visibility. The most significant advantage is the universal frame. It allows producing various types of passenger transport, including diesel, compressed or liquefied gas, and electric-powered versions. While these new features may not be visible to passengers, they are crucial for buyers.
By 2027, the plant will assemble passenger vehicles of the second and third generations, and then switch to the production of buses of the third generation only.
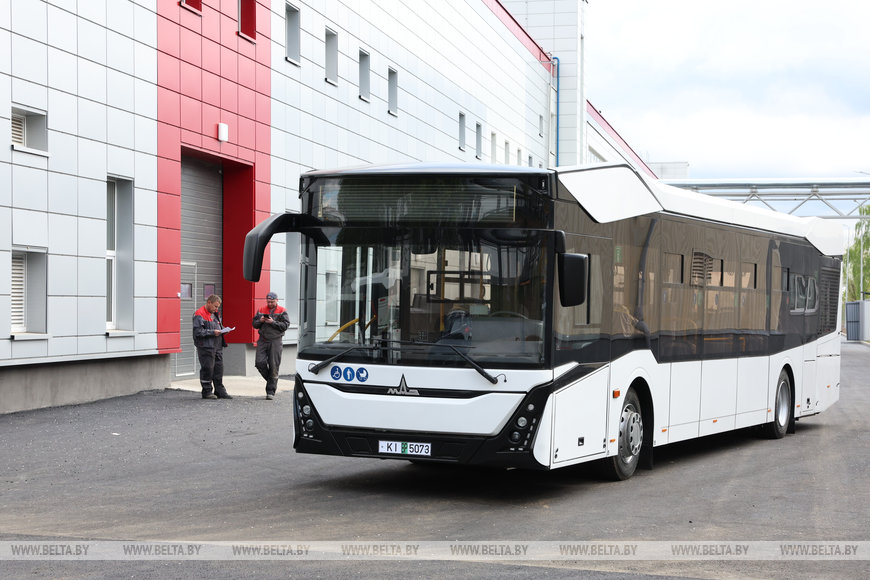
"This new-generation model, the MAZ 303, features enhanced equipment, smoother handling, and a more powerful engine. It is comfortable for both drivers and passengers. The climate control system is excellent. Modern instrument panel. It indicates when doors are open and alerts to any potential faults. Its electronic modules display a green light when functioning correctly. If an issue arises, they turn red," test driver Aleksandr Levdorovich shared his impressions.
Belarus and Russia remain the main sales markets for MAZ. But the task to diversify exports could not be ignored by the enterprise. This year the plant intends to significantly increase supplies to distant countries.
"We do not have a stockpile of unsold vehicles: we produce strictly on order. Every vehicle built in our workshop is already sold. This year, our goal is to deliver over 2,000 units, a fully achievable target. At present, we are filling orders for the third quarter. We have projects and signed contracts with several Latin American, African, and Asian countries. In 2025, we expect a significant increase in exports to distant markets," Vladimir Dormash, deputy commercial director for passenger vehicle sales, said.
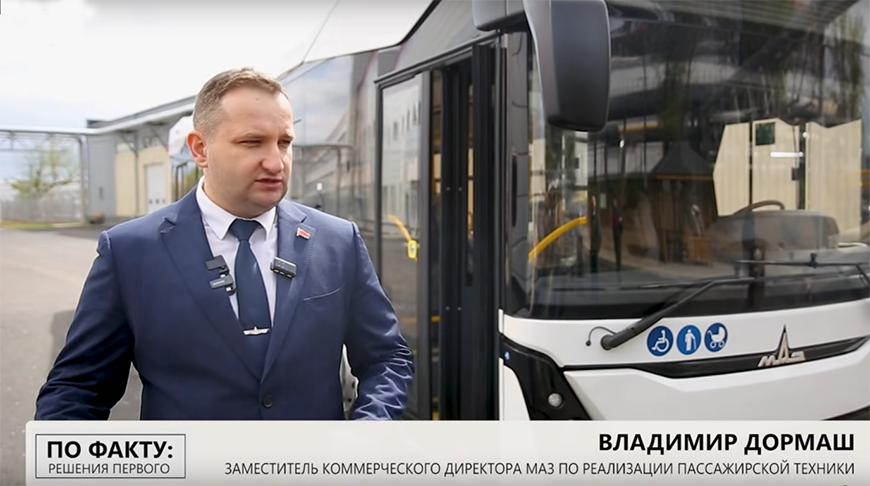
What did Lukashenko call his main presidential task?
At the beginning of the year, during his visit to the new bus manufacturing facility, Aleksandr Lukashenko recalled his previous visit to MAZ. According to him, the conditions the factory staff used to work in were in need of improvement. Didn’t they deserve their own modern factory? The head of state promised to have such a facility built if there is demand for Belarusian buses.
"They say you are on the up and up, and I will be delighted if this presidential project succeeds. I was determined to preserve our industry giants. When my tenure as president just began, I promised myself to preserve everything that had been built by previous generations. And those of you who are older remember: we set off on this big journey together. MAZ, BelAZ, elevators in Mogilev, Integral (its products are in huge demand today), and all other enterprises - all this had to be saved. Frankly speaking (again, I do not want to overpraise you), when I see a MAZ vehicle, our buses, trolleybuses, I feel pride. And I am happy that we have preserved the mechanical engineering industry in our country," the president noted.
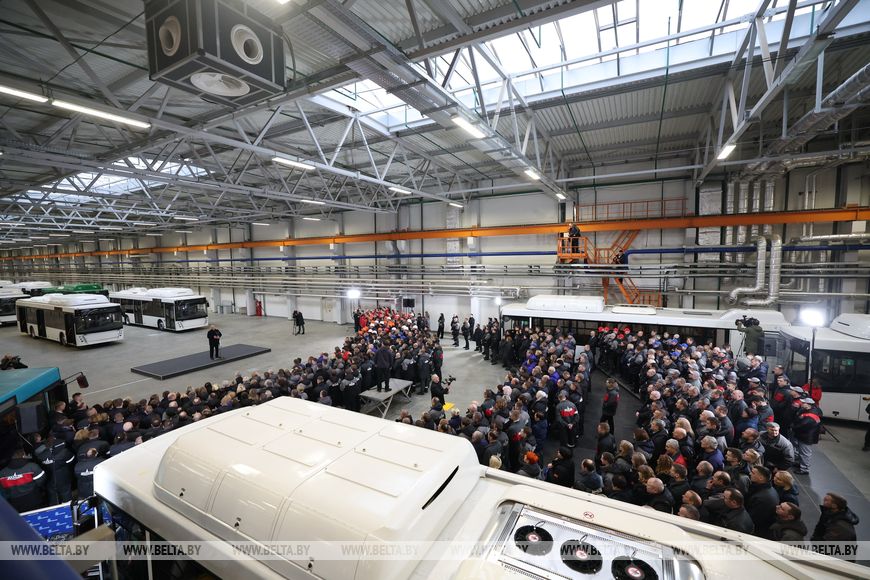
The inauguration of the new MAZ production facility marks not just an expansion in manufacturing capacity but a leap forward in Belarusian engineering. Aleksandr Lukashenko reassures that the state will continue supporting such enterprises, but only if results are delivered.
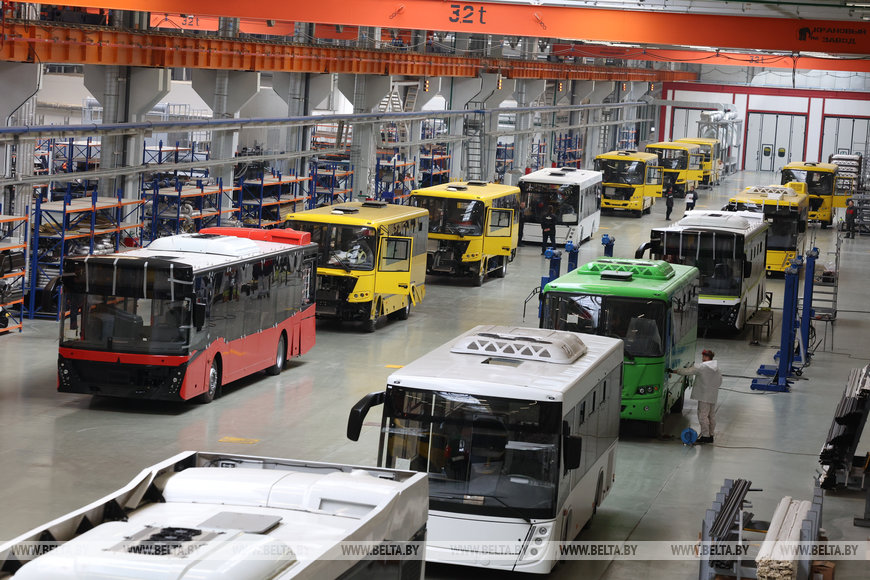